The aerospace industry has embarked on a rapid journey towards digitalisation, embracing the principles of Industry 4.0 by integrating emerging technologies into its industrial processes. Among the myriad of technologies, those showing the most promise for extensive industrial application include 3D manufacturing, robotics, augmented reality, Artificial Intelligence (AI), and digital twin simulation. The aerospace industry, being a high-tech sector, is best suited to reap multiple benefits from such emerging technologies. This article categorizes these technologies into two primary domains – manufacturing and software.
Within the manufacturing domain, 3D manufacturing and robotics stand out as pivotal technologies enhancing industrial setups by improving accuracy, production rates, and cost-efficiency. For example, aircraft Wind Tunnel Test (WTT) models are now produced through 3D printing, achieving high precision and simplicity in processes traditionally marked by complexity and high costs. Similarly, robots are being extensively used for repetitive tasks like aircraft riveting, fastening, welding, painting and inspection. This automation not only saves substantial man-hours but also elevates quality, with reports indicating a time-saving of approximately 20% from automating these tasks.
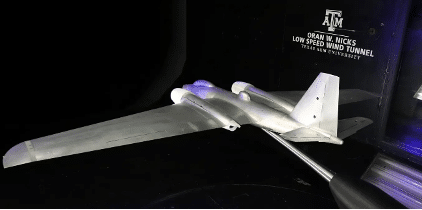
Figure 1: 3D Manufactured WTT Model
In the software domain, AI and Simulation are key areas with big data as their raw material. One such AI application is the Integrated Vehicle Health Management System (IVHMS) which uses AI algorithms-based data-driven decisions for predictive maintenance of aircraft which is more user-friendly and accurate for safe flight and currently in use on many aircraft like F-35 or JF-17 aircraft. Another significant software application is the ‘digital twin’, a virtual replica of a physical aircraft that serves as an valuable tool for prototyping, diagnostics, fatigue testing and fleet life cycle management. This technology offers cost-effective monitoring techniques, enhancing efficiency and predictive maintenance. Similarly, Augmented Reality (AR) is a powerful tool for training pilots, engineers, and technicians involved in aircraft operations and maintenance. It seamlessly combines the digital world with the real environment, resulting in reduced training time and expense, while enhancing the effectiveness of the instructions. Companies have reported up to 30% reduction in maintenance time by leveraging AR real-time information techniques.
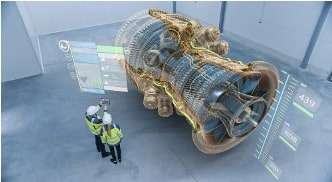
Figure 2: AR Technology
Although emerging technologies offer numerous advantages to the aerospace industry, there are significant challenges that come with them. Firstly, digitalisation is a costly endeavour that requires substantial expenditure in obtaining equipment, software, data centres, and frequent software updates. This level of investment may not always be feasible for small enterprises. Secondly, the process of digital transformation necessitates digital talent which is either not easily available in the market or very difficult to retain due to brain drain. Lastly, digitalisation in the aerospace industry is focused on data and hence, vulnerable to cyber-attacks for which potent cyber security management systems would be mandatorily required considering flight safety as the foremost priority of the aerospace industry. All of these challenges are real and comprehensible, but it is vital to acknowledge that without digital transformation, both traditional and emerging industries will struggle to sustain themselves. As a way forward, small enterprises could adopt the Block Building Approach which offers a viable strategy for investment, hiring digital talent and ensuring the seamless integration of current work ethics and practices.
Within the framework of Pakistan’s aerospace sector, it is important to implement comprehensive measures that guarantee the indigenisation and digitalisation of every phase of aerospace Design, Development and Production. Although Pakistan has made significant strides in the domain of aerospace production, there is still a need for improvement in the Design and Development side, which is facing multiple challenges including the retention of qualified human resource and financial constraints. However, this is achievable through the implementation of a comprehensive self-reliance policy at the national level. Such a policy should be aimed at indigenisation and digitalisation of the current aerospace industrial infrastructure in order to enhance competitiveness on the global stage and save foreign exchequer that is presently consumed towards foreign procurement. Insights may be drawn from China’s ‘Made in China 2025’ policy, which focuses on smart manufacturing technologies and digital transformation of ten critical industries, including the aerospace industry.
To conclude, the global aerospace industry has already begun to embrace digital transformation by integrating emerging technologies. This shift towards modernising outdated sectors is essential for future success and sustainability. In addition to lowering production costs, this can boost product performance and quality, positioning companies to be competitive in the international market. Pakistan, like many other nations, must undertake measures to transform its aerospace industry, among which the formulation of a national-level policy to facilitate ‘Industrial Digitalisation’ is a most critical aspect.
Raza Haider is a retired Air Commodore, currently serving as Director at the Centre for Aerospace & Security Studies (CASS), Islamabad, Pakistan. The article was published in The News International. He can be contacted at: [email protected].